Blog
3 Fundamental Advantages Of Mig Welding
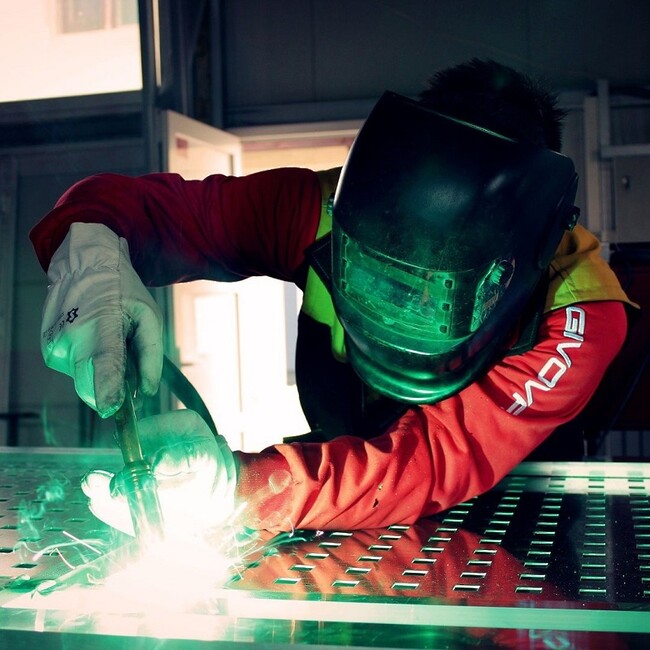
Those working with automotive chassis or construction would have used or come across a Mig welding machine. Metal-Inert Gas welding, or Mig for short, is a process where an arc is formed between the electrode and the surface to be welded. To protect the welded metal from atmospheric contamination, the process uses a shielding gas.
MIG welding is one of the most common and versatile forms of welding, as it offers a multitude of benefits. 3 such merits will be discussed below.
Benefits of opting for MIG welding.
Speed
When compared to other forms of welding such as friction, electron beam, laser or others, MIG welding is touted to be the fastest. The reason behind this speed is due to the continuous feeding of the electrode. Moreover, welds are usually more accurate when the time taken is minimal. Thus, the speed also ensures an improved accuracy, making this form of welding ideal for even less-experienced technicians.
Deep Penetration
When it comes to welding, the depth and strength of the weld matter. MIG welding offers this distinct advantage, providing a tough, continuous bead. This powerful arc also translates to more versatility. MIG welding can be performed on a variety of metals of different thicknesses such as magnesium, mild steel, aluminum and more.
Fewer Halts
One of the biggest disadvantages of a method like TIG welding is the continuous need to start and stop the welding process. Each time this happens, electrodes might have to be changed and other calibrations would also need to be done, thereby increasing production time. With MIG welding, however, the electrode is fed-continuously, thus the welding process can be seamless, and there are very few halts if any.
A premium welding supply store based out of Port Colborne and Stoney Creek, Ontario, we at Lock 8 Equipment stock a multitude of welding-related parts and machines. We even offer rentals on premium welding machines. To know more about our products and services, contact us today.