Blog
7 Most Common Welding Defects and Ways to Prevent Them
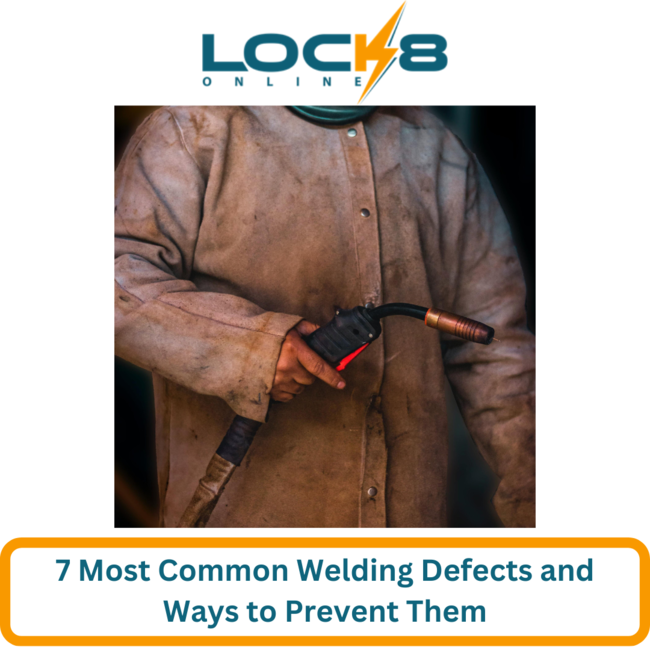
Welding defects are common even among experienced welders as it takes a lot of time and experience to lay perfect welds. However, not all defects are considered irremediable. In this blog, we will learn about welding defects and review some of the most common ones. But first, let’s have a look at what a welding defect is.
What Is a Welding Defect?
A welding defect is a flaw that can compromise the quality of the weld seam and the overall stability of the welding structure. Depending on the type, size and location, welding defects can be accepted or rejected by the inspector. All welding flaws have features of discontinuities. When these features exceed the accepted ISO 5817 and ISO 10042 standards, they become a defect and end up being rejected by inspectors.
A weld defect can weaken the weld joint and affect its aesthetic look. There are several types of welding defects. Professional and beginner welders need to constantly refine their skills as well as use proper welders' equipment to minimise the chances of welding defects.
Most Common Welding Defects
Inclusions
Inclusions are particles trapped in the weld pool. They can be metallic (tungsten, copper or other metal) or non-metallic (sulphide and oxide). Inclusions usually result from incorrect manipulation of the electrode, incorrectly set welding parameters or poor storage of welding consumables. To avoid inclusion, make sure your welders' equipment is properly calibrated. Ensure the base metal is well cleaned before welding, avoid low amperage settings, keep a proper torch speed and try to clean slag from previous welds between passes.
Porosity
Porosity is another common welding defect. Porosity is when gas bubbles accumulate and get trapped inside a weld. Various gases form and evaporate during welding. However, if these gases are trapped, they become a part of the weld and can weaken the joint. To avoid porosity in your welds, clean the base metal properly. If using welding consumables, ensure the electrode coating is not damaged. If you use welding gas, make sure to set the flow correctly. Lastly, move the torch slowly enough to keep a molten paddle while allowing the gas to bubble out.
Cracks
Cracks are the most severe form of defects. Aside from substantially weakening the weld, it can lead to the complete failure of the structure. Cracks occur as a result of incorrect termination of the arc, high welding currents, excessive joint restraint and incorrect selection of the consumable.
Lack of fusion
Lack of fusion is when the weld seam has gaps or voids or when the quality of fusion with the base metal is poor. Some of the precursors of poor fusion are the incorrect size of the electrode used, the torch being moved too fast or low amperage. Lack of fusion negatively affects the quality of the weld and can lead to failure of the welded structure.
Undercut
This welding defect appears as a dent at the edge of the weld, either on the top or bottom of the weld. Undercut generally occurs from too high welding current or travel speed or incorrect operator technique.
Underfill
Underfill occurs when the weld joint sits below the base metal. In the case of an underfilled weld, the joint is thinner than the base metal, making the weld seam weak. To avoid underfilled seams, try not to move the torch too fast and use the correct size of the electrode as well as the correct current rating.
Burn through
Burn-through happens when too much heat is applied during the welding. Burn-through is essentially a hole created between the two pieces of base metal. Burn-through occurs from incorrect welding settings, when the gap between the metal pieces is too large or when the torch moves too slowly. This defect is usually encountered with thin material less than 1/4 inch thick. It can also occur with thicker stock if your welder settings are too high, if the gap between pieces is too large, and/or if you are moving the torch too slowly. To avoid a burn-through during welding, ensure your welders' equipment is properly calibrated, e.g. the current rate is appropriate for the type of metal. Apart from that, make sure the gap between the workpieces is not too large and the travel speed is not too slow.
Welding is not an easy skill to learn. It takes a certain set of skills and experience to lay perfect welds. It is also important to use proper and quality welders’ equipment and welding consumables to achieve good results. Lock 8 is a trusted welding supply store with locations in Port Colborne and Stoney Creek in Ontario, Canada. We offer a wide range of quality welding supplies as well as welding equipment for sale and rent. Contact us today to inquire about a product or to set up a demo in one of our locations.