Blog
A Comprehensive Guide To Choosing Your First Welding Machine
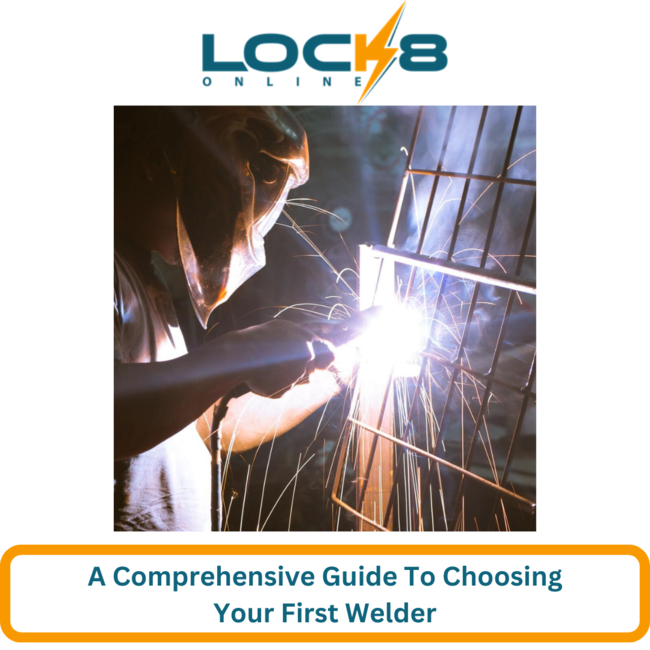
Taking its origins in the XX century, today welding has evolved into a highly technological industry that serves sectors such as metal fabrication, construction, transportation, manufacturing and more. It is barely possible to find an industry where welding is not applied.
The welding equipment market is immense, and just like different car makes are presented on the market, there are different welding machines available for both beginner and experienced welders to choose from.
As buying a welding machine is, in a way, an investment, let’s have a closer look at the different factors that need to be taken into account when shopping for a first welding machine. This guide will be useful for both beginners and proficient welders alike.
A Comprehensive Guide To Choosing Your First Welding Machine
Types Of Welding Methods
Before we discuss the aspects to consider when shopping for a welding machine, let’s have a quick overview of the different welding methods used in welding.
MIG Welding
MIG, or Metal Inert Gas welding, or GMAW, is an arc welding method where a wire welding electrode on a spool fed automatically at a constant pre-selected speed is used. The arc is created by an electrical current. The arc melts the wire and the base metal, joining them and creating a high-strength weld. A MIG welder is used when working with both thin and thick metals and is great for welding steel, aluminum and stainless steel.
In MIG welding, a shielding gas is flooded over the weld to protect the weld area from atmospheric contamination. The shielding gas used with the MIG welding machine is usually carbon dioxide.
TIG Welding
When welding with a TIG welder, a non-consumable tungsten electrode produces the weld. A long rod made of filler metal is fed into the weld puddle. While the metal rod is consumed by the weld puddle, the role of the electrode is that of a flame torch - it only strikes and maintains the arc to melt the metal.
Much like MIG, TIG welding uses a pressurized inert gas (usually argon) to flood the weld area to protect it from contaminants.
TIG welding is a little more difficult to master than any other welding method as it requires the welder to use both hands (to handle the torch and to feed the filler metal). However, the welds produced with TIG welders are usually stronger and are of better quality.
Stick (or SMAW) Welding
In contrast to MIG and TIG, which use shielding gas to protect the weld pool, stick welders use a consumable stick electrode coated with flux. The flux melts and releases gasses that shield the weld area. The diameter of the welding rod is selected according to the thickness of the metal to weld.
Welding with a stick welder is generally easy to master and can even work on dirty or rusty metals. However, stick-produced welds require extensive post-welding byproduct cleaning.
Flux-cored Welding
FCAW welding uses a hollow, tubular electrode filled with flux rather than a solid metal electrode.
Depending on the shielding methods, flux-cored welding can be self-shielded or dual-shielded. In self-shielded FCAW welding, the actual flux core wire protects the weld puddle. In dual-shielded FCAW welding, the weld pool is protected by an external gas in addition to the flux core wire.
What Are Multiprocess Welding Machines?
Multi-process welding machines can weld multiple methods. The main advantage of such welders is that they enable welders to carry out different welding jobs without switching the power source. For instance, Forney multi-process welder is capable of welding steel, stainless steel, cast iron and aluminum (with a spool gun) and can tackle multiple welding tasks in construction, fabrication, shipbuilding and other heavy-duty applications.
Multi-process welding machines may cost more than single-process welders. However, they are worth the investment as they allow welders to save time and especially money in the long run.
While multi-process welders have various applications, they are found to be the most useful in small to medium shop and home-based welding projects.
Aspects To Consider When Choosing Your First Welder
1. Choose a welder according to the type of metal you will be working with
Every welding machine is suitable for welding specific metals. Aluminum is one of the most common metals used in manufacturing. It is also one of the metals difficult to master for welders. Aluminum has an oxide layer that melts at a significantly higher temperature than the aluminum underneath it. Welders must take this into account in order to avoid burnouts of the aluminum underneath the oxide layer.
Refer to the Chart 1 for quick reference on the types of welding methods and materials they are fit for.
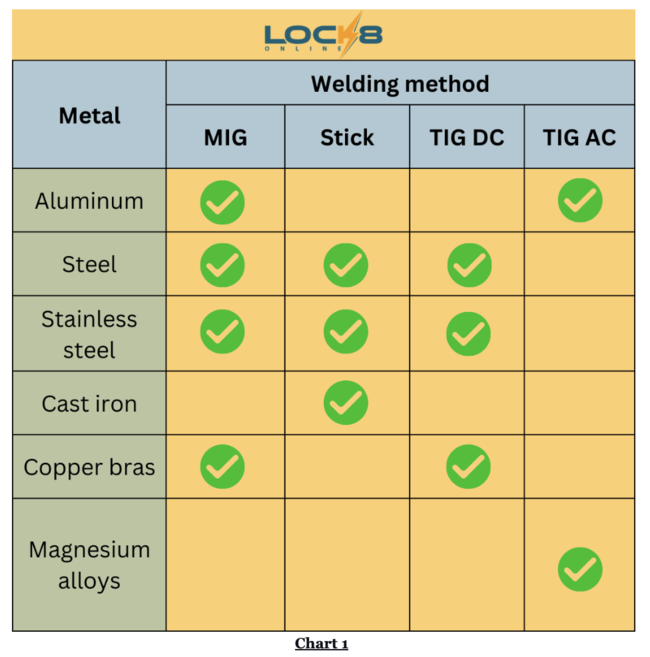
If you plan on working on multiple projects involving various metals, a multi-process welder like Lincoln Flextec 350X Powerconnect is a good welding machine to opt for.
2. Establish a current range that covers all possible metal thicknesses
Thicker metals require more current to ensure good penetration.
Thin metals, on the contrary, need lower heat and amps. Welding thin metals is a pretty sensitive job as it is important to supply just enough heat to avoid weakening or melting of the metal.
The cost of a welding machine majorly depends on how much current it generates and how deep into the metal it can penetrate, so it is important to know in advance the thickness of the metal you will be working with most of the time.
3. Consider the power supply in the welding location
The type of welder you choose also depends on the power supply of the location where you plan to work from. To complete your welding projects from home or a small welding shop, opt for a welder with 120V input power. For use in industrial settings, a heavy-duty welder with 220/240V input power is required. If most of your projects are completed in remote locations where access to the power grid is limited, an engine-driven portable welding machine or a power generator is required.
If you plan on running your welder on a power generator, look for the CC (constant current) and CV (constant voltage) symbols. Constant voltage is a feature of semi-automatic and wire-fed welding processes (like MIG or flux-cored arc welding). CV welders provide a consistent preset voltage which is important for maintaining a constant arc length as the arc length is directly related to weld voltage.
The quality of welds also depends on the weather conditions. Welding in windy conditions is another challenge welders face when working outdoors. The shielding gas, which is used to shield the weld puddle from air contaminants, gets blown away, resulting in oxidation and porosity and making MIG welding ineffective in windy conditions.
In breezy conditions, where the use of a MIG welder poses lots of challenges, you want to have an option within your welder to use reverse polarity and a gasless flux-cored wire, as the flux-coated wire shields the welding puddle, so no gas is required.
4. Compare the features
When shopping for your first welder, the following key features are the most important to consider:
- Duty cycle. The duty cycle is the amount of time in a 10-minute period that the welder can weld at the highest current of the machine. Once that time limit is hit, the welder needs some time to cool down. It is recommended against exceeding the duty cycle as the circuits inside the machine may burn out. Sometimes, the duty cycle is expressed in percentage. For hobby welding, a 20% duty cycle is enough, for medium-duty 40-60%, and for heavy-duty 60-80%.
- Open-circuit voltage. Open-circuit voltage is the voltage coming from the welding torch when there’s no current flowing to it. While working around an open circuit is dangerous, open-circuit voltage is what helps to strike the arc more effectively.
Some organizations, like American National Standard for Arc Welding Equipment, limit the open-circuit voltage on welding equipment for safety reasons. This is something to consider for novice welders as striking the arc is a skill beginner welders have difficulty mastering.
- Thermal overload protection. This feature is important to protect the welder from overheating. The thermal overload protection mechanism shuts the output power to your torch if the circuit starts overheating, and the cooling mechanism will continue dispersing the heat. Ask your sales representative how the welder of your choice is protected from overheating. At Lock 8, we are always ready to guide you on all our welding equipment and help you select the right type of welder.
Wrapping It Up
Choosing the first welder is not an easy task. You need to know your goals well and be familiar with many aspects, such as the available power supply at the location you work and how this impacts your choice of welder, types of welding methods suitable for various metals and so on. If you feel like you can’t grasp everything at once, you can always reach out to a welding supply store and ask for guidance from a professional. Some welding supply stores, like Lock 8, offer their clients an option to test out a welder before buying it. This is great for buying your first welder as you get to test several machines and see their work in action. Lock 8 is a trusted welding equipment and accessories supplier with locations in Port Colborne and Stoney Creek, ON Canada. We are always happy to guide our customers on various types of welding equipment and help them choose the right machine for their needs. Since 2007, we have served industrial clients, professional welders, and beginner welders alike. Apart from offering welding equipment for sale and rent, we also give our clients an option to purchase quality refurbished welding equipment. Whether you are a hobby welder in need of a simple and easy-to-use welding machine or a contractor looking for welding equipment to supply a major construction project, at Lock 8, you can find all the necessary quality equipment. Reach out to us today and speak to one of our experts in welding equipment.