Blog
MIG vs. Stick Welder - 4 Key Differences Explained
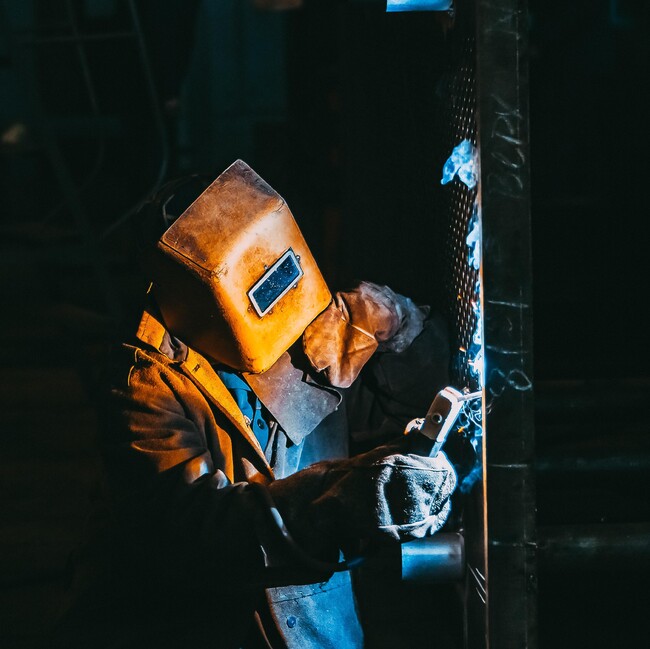
Welding is widely used in metal fabrication. There are several welding processes and each is deployed depending on factors like the type of steel to be fused, the welder’s experience, specific project requirements etc. In this blog, we shed light on MIG welders and stick welders as well as discuss some key criteria that make MIG and stick welding different.
MIG GMAW welding overview
MIG welding is an arc welding process where a wire electrode is fed into the weld pool, melting the base metals and fusing them. An important component of MIG welding is the shielding gas which is used to protect the molten pool of metal from potential reaction with atmospheric elements.
Stick SMAW welding overview
In Shielded Metal Arc Welding (or stick welding), an electric current, typically DC, creates heat that melts both the electrode and the base metals. The electrode is consumed into the weld fusing the pieces of base metals together.
Difference between MIG and stick welding
The shielding gas is what sets these two welding processes apart. MIG welding uses an external gas source to protect the weld from atmospheric contamination, whereas the stick welding process is gasless. In stick welding, the joint is protected by the vapours released from the flux coating disintegrated from the electrode.
Outdoor/indoor application
Given that MIG uses a shielding gas to protect the weld from atmospheric contamination, it is not suitable for welding outdoors as bad weather can affect the quality of the weld. Stick welding, on the contrary, works perfectly outdoors and underwater.
Weld quality
Stick welding produces spatter and slag from the electrode disintegration which may considerably affect the joint quality. MIG welding, in comparison, produces cleaner and tidier welds.
MIG welding is pickier in terms of the welding process setup as it requires the metal to be thoroughly cleaned. The quality of the weld can be seriously affected if the metal is not properly cleaned from dirt or corrosion. Stick welders, however, can work through dirt, paint or rust.
Ease of use
While both processes are easy to use, MIG welding is considered easier to pick up for novice welders. MIG welding is also considered semi-automatic as the welding speed and wire position are controlled manually whereas the wire feed rate and arc length are controlled by the power source. Stick welding is more complex as the welder needs to manually apply filler metal.
Stick welders are also easier to transport because they do not use a shielding gas, so there is no need for an external gas cylinder.
Metal thickness
Stick welders perform better on thicker metals due to their better penetration abilities. MIG welders can weld both thin and thick metals. MIG is a common welding method used to weld aluminum, stainless steel, carbon steel, copper, nickel and bronze.
Stick welders are also easier to set up as they consist of an electrode, electrode holder and cable, power source and earthing clamp. MIG welders, on the other hand, have more variables to consider, such as gas type, nozzle type and nozzle tip.
Even though stick welders are considered easy to set up and relatively easy to operate, the stick welding process requires advanced skills to lay high-quality welds.
Both welding processes are widely used in various applications. Depending on the welding project, each process offers more advantages than the other. The primary aspects welders need to consider when choosing a welding machine are the type of metal to weld, the environment (indoors vs. outdoors), and whether they need to travel much between job sites.
Lock8 is a trusted welding supply store offering a range of welding solutions for industrial clients and contractors. With locations in Port Colborne and Stoney Creek, ON, we offer welding equipment both for sale and rent. Get in touch with us today to learn about other types of industrial equipment we offer.