Blog
Role of AC & DC Outputs in MIG, TIG And Stick Welding
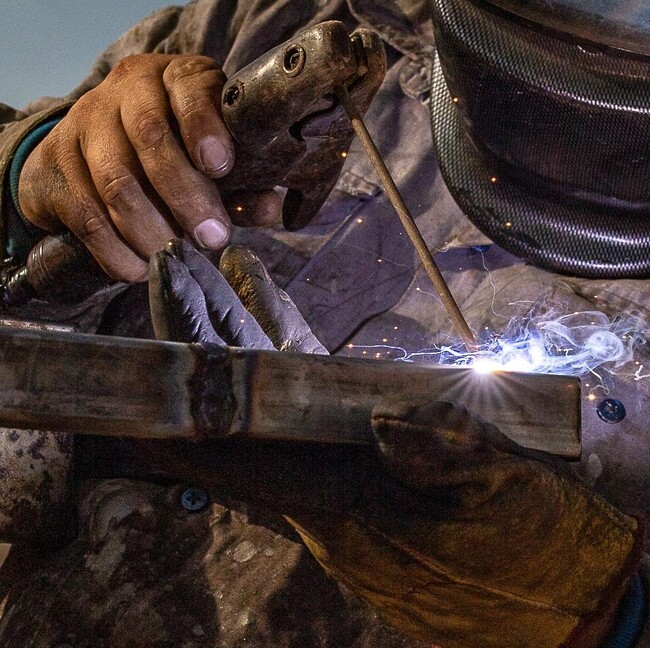
Welding machines can use alternating and direct currents (AC &DC), which can sometimes be confusing for beginners and experienced welders alike. This blog will review what AC and DC currents are and their differences in terms of application with various welding methods.
AC & DC overview
In AC output, the current constantly switches its direction back and forth. The electrode holder/MIG/TIG torch and the ground clamp switch polarity many times per second.
In DC output, the electric current flows in a single direction. To keep the electricity flowing, a ground clamp and an electrode holder or a TIG/MIG torch are used to complete the circle. The arc bounces between the electrode and the metal with the ground clamp attached, completing the electrical circuit. Because the magnetic field and current of the arc are constant, DC welding produces stable arcs.
Differences between AC and DC in welding
The essential difference between AC and DC is that AC output switches the polarity, and the current constantly flows back and forth whereas DC output keeps the polarity uniform, and the current flows in one direction.
The current in DC output can be electrode negative (or DCEN for short) or electrode positive (DCEP). In DCEN mode, the ground clamp is positive and the electrode is negative. In this case, the electrode receives less heat than the metal (~30% to 70% ratio). In DCEP mode, the ground clamp is negative and the electrode is positive and the ratio is reversed (the electrode receives more heat).
How AC and DC work with different welding methods
TIG Welding
AC TIG Welding. TIG welding method with AC output is best to weld aluminum. It uses alternating positive and negative cycles. The positive cycle destroys the oxide level on the surface of the aluminum. When the oxide level is eliminated, the negative cycle penetrates the actual metal altogether creating a high-quality weld seam.
DC TIG Welding. In DC output, the current flows in one direction. DC output can be of negative (DCEN) or positive (DCEP) polarity. Because in DCEN welding, the welded metal receives about 70% of heat, this process is good for deeper weld penetration. DCEN is most commonly used in TIG welding when the cleaning action of the DCEP process is not needed.
Because in the DCEP process, 70% of heat is concentrated in the electrode, the use of the DCEP process in TIG welding requires larger diameter electrodes to prevent the electrode from heating or melting. DCEP is less efficient as it provides lower penetration levels. DCEP is rarely used in TIG welding and it is mostly used as a part of the cycle in AC welding.
DC TIG welding is used for joining mild steel, stainless steel, and carbon steel.
MIG Welding
AC MIG Welding. AC MIG welding is rare as the constant change of current makes AC MIG a less reliable welding method compared to, for instance, DC TIG or DC MIG. AC MIG welding is used in processes such as cold metal transfer welding and AC aluminum pulse. Direct current is used in MIG welding far more often than alternating current.
DC MIG Welding. Electron positive (DCEP) polarity is recommended for MIG welding. MIG welding with negative polarity is challenging and results in unstable arc and a messy weld.
Stick Welding
DC Stick Welding. Stick welding is mostly used with DC output. Here, the choice of polarity plays an important role in achieving a quality weld. DCEP polarity is mostly used when stick welding. When the electrode is subjected to high temperature, the droplets of the melting electrode are propelled into the welded metal penetrating deep into the weld joint.
Understanding the difference between AC and DC welding processes is important when deciding what type of welding machine to use for a specific project or when shopping for a welding machine. At Lock8, we are here to advise you on different welders offered at our welding supply store to make sure you walk away with welding equipment that best suits your needs. Get in touch with us today.